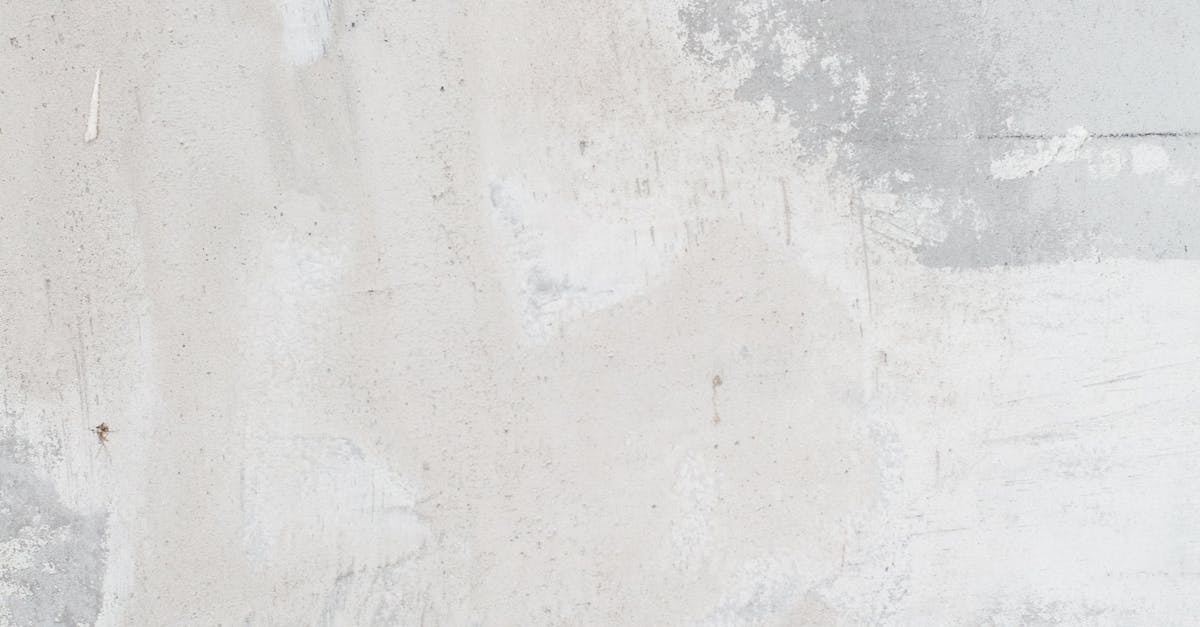
Factors to Consider When Choosing an Accelerator
When selecting an accelerator for concrete, it is crucial to consider the specific application and environmental conditions. Accelerator admixtures not only enhance the setting time but can also influence the overall strength and durability of the concrete. Factors such as temperature, humidity, and project timelines play a vital role in determining the most suitable product. Understanding the compatibility of the accelerator admixture with other mix components will help achieve the desired results without compromising the integrity of the concrete.
Another significant aspect to think about is the type of accelerator being used. There are various formulations, including calcium-based and non-chloride types, each with its unique benefits and potential drawbacks. For instance, while calcium-based accelerators can effectively speed up the curing process, they may also increase the risk of efflorescence in some environments. Evaluating the long-term performance characteristics of the accelerator admixture is essential for ensuring that it meets project standards and expectations.
Climate and Temperature Impact on Accelerator Performance
The impact of climate and temperature on the performance of concrete accelerators is significant. In colder weather conditions, traditional curing processes may slow down, making the use of accelerator admixtures essential to achieving desired setting times and strength development. Low temperatures can hinder the hydration process, leading to longer time frames for concrete to reach its full potential. As a result, using an accelerator admixture becomes vital in maintaining efficiency and ensuring early strength gains in winter or cooler environments.
Conversely, high temperatures can accelerate the curing process too quickly, which may lead to issues such as plastic shrinkage cracking or a reduction in workability. In hot weather, careful selection of an accelerator admixture can help manage these challenges by balancing setting times while allowing for sufficient workability during application. Understanding the specific environmental factors is crucial for optimizing the performance of accelerator admixtures and achieving the desired outcomes in concrete projects, regardless of the climate.
Mixing Guidelines for Concrete Accelerators
When incorporating an Accelerator Admixture into concrete mixes, precision is key. It is essential to follow the manufacturer’s guidelines regarding the specific dosage. Typically, the amount of accelerator used can range from 1% to 5% of the weight of cement. Adjusting the dosage depends on various factors such as temperature and the desired setting time. Overuse may lead to unforeseen side effects like excessive heat generation or reduced workability.
Mixing should be thorough to ensure an even distribution of the Accelerator Admixture throughout the concrete. Begin by adding the dry components, followed by any required water, and then introduce the accelerator. This method helps prevent clumping and promotes optimal integration into the mix. Continuous mixing is recommended for at least five minutes to achieve uniformity. Proper mixing is vital for maximizing the performance benefits of the accelerator while maintaining the desired properties of the concrete.
Recommended Ratios for Effective Use
When using an Accelerator Admixture, determining the optimal dosage is crucial for achieving the desired performance in concrete. Typically, manufacturers provide guidelines that recommend adding between 1% to 2% of the weight of cement. This ratio can vary based on specific product formulations and environmental conditions. It is essential to review the product data sheets and conduct preliminary tests to ascertain the ideal amount for your particular mix, especially in extreme weather conditions.
Adjusting the ratio of the Accelerator Admixture may be necessary depending on the specific requirements of the project. For instance, in colder climates where rapid strength gain is essential, a higher dosage may enhance the curing process. Conversely, in milder conditions, sticking to the lower end of the recommended range might suffice. Monitoring the performance characteristics such as setting time and strength development is vital for fine-tuning the mixture to ensure optimal results.
Performance Testing of Concrete with Accelerators
Performance testing of concrete treated with accelerator admixtures is essential to assess the material’s strength and durability. Standard tests, such as compressive strength evaluations, are employed as benchmarks to determine the effectiveness of the chosen accelerator. Specimens are typically cured under controlled conditions to reflect the intended environmental exposure. Testing can be conducted at various intervals, with results compared against control mixes without accelerators to identify any significant differences in performance.
Durability tests are also crucial when evaluating the long-term implications of using accelerator admixtures. These tests often include freeze-thaw cycles, permeability assessments, and resistance to sulfate attack. The results provide insights into how well the accelerated concrete can withstand environmental impacts over time. Understanding these performance metrics helps in making informed choices regarding the optimal accelerator admixture for specific applications.
Methods to Evaluate Strength and Durability
Evaluating the strength and durability of concrete mixed with an accelerator admixture involves several standardized testing methods. Compressive strength tests are commonly conducted at specific curing intervals, such as 7, 14, and 28 days, to gauge the effectiveness of the accelerator in enhancing strength development. Flexural strength tests can also be performed to assess how well the concrete withstands bending and tension forces. These tests provide critical data on how various accelerator admixtures influence concrete performance over time.
In addition to strength testing, durability assessments are crucial in understanding the long-term performance of concrete containing accelerator admixtures. Tests such as water absorption, freeze-thaw resistance, and sulfate resistance can reveal how well the concrete will hold up under environmental stresses. Observing the effects of the accelerator admixture on these durability properties helps ensure that the concrete meets the required standards for its intended application.
FAQS
What is a concrete accelerator?
A concrete accelerator is an additive that speeds up the curing process of concrete, allowing it to reach its desired strength more quickly.
What factors should I consider when choosing a concrete accelerator?
When choosing a concrete accelerator, consider factors such as the climate and temperature, the type of concrete mix, application timing, and the desired strength and durability of the finished product.
How does temperature affect the performance of concrete accelerators?
Higher temperatures typically enhance the effectiveness of concrete accelerators, while lower temperatures can slow down the curing process. It’s essential to choose an accelerator suitable for the specific climate conditions of your project.
What are the recommended mixing guidelines for using concrete accelerators?
Recommended mixing guidelines include adding the accelerator to the mixing water and ensuring thorough mixing with the dry materials. The specific ratios vary by product, so always refer to the manufacturer’s instructions for optimal results.
How can I test the performance of concrete with accelerators?
The performance of concrete with accelerators can be tested through various methods, including evaluating its compressive strength using standard cylinders, conducting durability tests, and assessing the time taken to set compared to standard mixes.