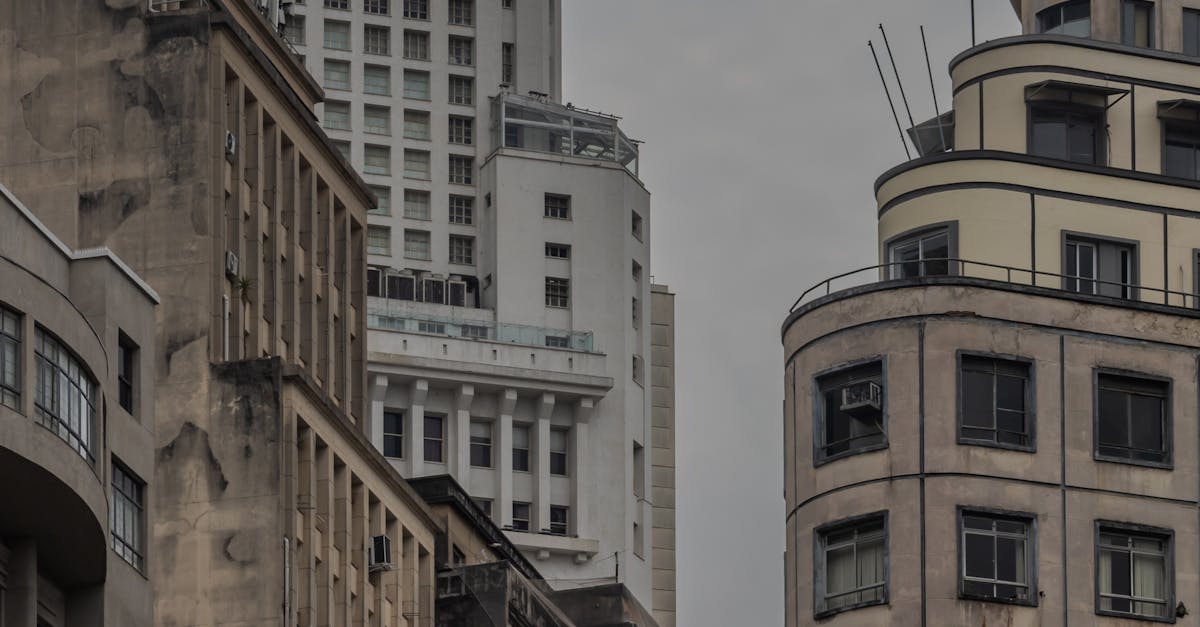
Quality Control in Ready Mix Concrete
Quality control in ready mix concrete is crucial for ensuring that the final product meets the required specifications and standards. Each batch is prepared in a controlled environment, allowing for precise measurement of ingredients. Quality control measures include frequent testing of materials and the final mix, which helps in identifying any inconsistencies early in the process. This systematic approach minimizes the risk of defects and enhances the performance of the concrete in various applications.
In contrast, onsite mixed concrete may face challenges related to quality control due to varying environmental conditions and the potential for human error. The mixing process can be influenced by factors such as temperature and moisture levels, which can affect the consistency and strength of the concrete. Consequently, ready mix concrete tends to provide a more reliable solution for projects that demand strict adherence to quality specifications. The ability to maintain quality in a controlled environment gives ready mix a distinct advantage over onsite mixed concrete.
Standards and Testing Procedures
Quality control in concrete production is essential for ensuring that the final product meets specific standards and performs as intended. Ready mix concrete facilities adhere to stringent testing procedures, which include regularly checking the composition of aggregates, cement, water, and admixtures. These facilities often follow guidelines set by organizations such as ASTM International to maintain consistent quality throughout the batching process.
Onsite mixed concrete, while offering some flexibility in adjusting mixes to suit project specifications, can be at a higher risk for variability. The quality largely depends on the skill and experience of the personnel mixing the materials. Regular testing, such as slump tests and compressive strength evaluations, is crucial to ascertain that the onsite mix adheres to desired performance criteria. Without rigorous oversight, the potential for inconsistencies in onsite mixing can lead to structural concerns over time.
Cost Comparison
When comparing the costs associated with site mix concrete and ready mix concrete, it’s essential to consider various factors. Site mix concrete often requires the purchase of raw materials and equipment for mixing on location. This can lead to additional costs such as labor and equipment rentals. However, the flexibility of adjusting the mix according to specific project needs may result in savings on materials if executed efficiently.
Ready mix concrete typically comes with a fixed price per cubic yard, which includes delivery and mixing. While this may seem higher initially, it eliminates many of the uncertainties linked to onsite mixed concrete. The experience and established procedures of ready mix suppliers can also lead to time savings, ultimately reducing the overall project cost despite the upfront price difference.
Analyzing Expenses of Site Mix vs. Ready Mix
Analyzing expenses related to site mix concrete and ready mix concrete reveals distinct considerations that can impact a project’s budget. Onsite mixed concrete typically involves immediate batching and mixing on the construction site, which can reduce transportation costs. However, this option might require additional labor, equipment, and site preparation, potentially increasing overall expenses. The variability in local labor rates and equipment rental costs can further influence the budget for onsite operations.
In contrast, ready mix concrete offers a more predictable pricing structure. This type of concrete is pre-mixed at a centralized plant and delivered to the site, streamlining the process. While there may be delivery fees associated with ready mix concrete, the elimination of onsite labor for mixing can balance out these costs for larger projects. Maintenance of quality is more consistent with ready mix, ultimately impacting the long-term expenses linked to repairs or replacements that may arise with inferior mixes from onsite batching.
Time Efficiency
Time efficiency plays a crucial role in construction projects. Ready mix concrete offers a significant advantage due to its quick delivery and immediate usability. When a contractor orders ready mix, the concrete is prepared at a centralized plant and transported to the project site, minimizing delays. This streamlined process allows workers to start pouring and forming structures without waiting for materials to be mixed on-site.
Onsite mixed concrete, in contrast, requires additional time for mixing and preparing the concrete right at the job site. This can lead to longer project timelines, especially in larger projects where multiple batches may be needed. Any delays in the mixing process can further impact the schedule. Therefore, while onsite mixed concrete may offer some flexibility, the overall time efficiency is generally lower than that of ready mix concrete.
Speed of Project Completion for Each Type
Speed of project completion often hinges on the choice between site mix concrete and ready mix concrete. Ready mix concrete is manufactured in a controlled environment and delivered to the site, allowing for immediate use upon arrival. This streamlined process reduces downtime significantly and supports rapid project progression, making it the preferred option for large-scale developments.
Onsite mixed concrete, while offering some flexibility in adjustments during the mixing process, can lead to delays. Mixing at the site may require additional time for preparation and cleanup. This aspect can hinder overall project speed, particularly if weather changes or equipment issues arise during mixing. Timely project completion could be affected if coordination or scheduling is not meticulously managed.
FAQS
What is site mix concrete?
Site mix concrete is made by mixing the raw materials—cement, aggregates, and water—on the construction site according to the desired specifications and proportions.
What is ready mix concrete?
Ready mix concrete is pre-mixed concrete delivered to the construction site in a truck, allowing for immediate use without the need for on-site mixing.
What are the advantages of using ready mix concrete?
Ready mix concrete offers several advantages, including consistent quality, time efficiency, reduced labor costs, and less space needed for materials on-site.
How does cost compare between site mix concrete and ready mix concrete?
While site mix concrete may appear cheaper initially due to lower material costs, ready mix concrete can save money overall by reducing labor expenses and minimizing waste.
Which type of concrete is more time-efficient?
Ready mix concrete is generally more time-efficient because it can be delivered to the site in a ready-to-use condition, speeding up the construction process compared to site mix concrete that requires on-site preparation.