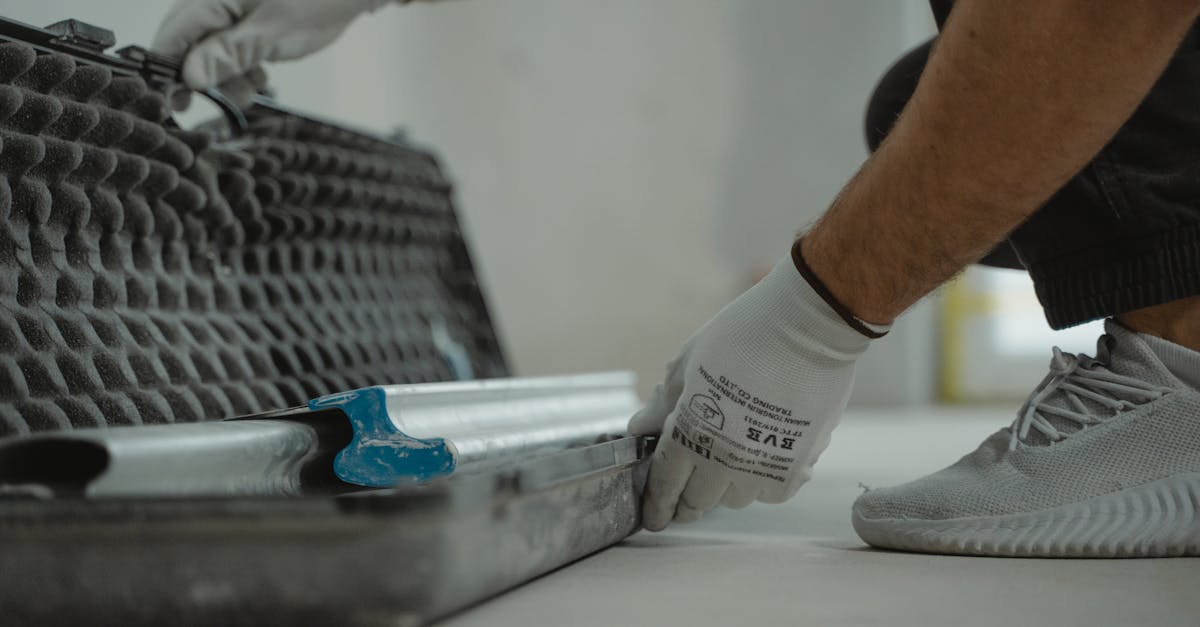
Equipment Required for Site-Mixed Concrete
Onsite mixed concrete in construction projects requires specific equipment to ensure efficiency and quality. Essential tools include concrete mixers, which can be either drum or volumetric types, allowing for consistent mixing at the site. Additionally, shovels, wheelbarrows, and trowels facilitate the transportation and placement of the mixed concrete. Other tools like measuring containers and mixing buckets play a crucial role in ensuring the right proportions of materials.
When it comes to machinery, larger sites may benefit from using a portable concrete plant, which provides better control over the mixing process. This equipment can produce high volumes of concrete quickly while maintaining the desired mix specifications. Furthermore, vibrating equipment helps remove air pockets during the pouring process, contributing to improved density and strength of the finished product. Proper equipment choice and maintenance contribute significantly to the overall performance of onsite mixed concrete.
Essential Tools and Machinery
Onsite mixed concrete requires specific machinery and tools to ensure efficient mixing and application. A concrete mixer is fundamental, available in various sizes and types, including drum and pan mixers. These mixers guarantee a consistent blend of cement, aggregates, and water. Additionally, a concrete pump can facilitate the transportation of the mixed concrete to hard-to-reach areas, promoting effective placement and reducing labor efforts.
Other essential tools include shovels, trowels, and wheelbarrows, which aid in the handling and application of the concrete. Proper measuring equipment, such as scales and graduated containers, ensures proportions are accurate for the desired concrete strength. Onsite mixed concrete in various projects depends on the reliable operation of these tools and machinery, leading to effective workflow and quality results.
Quality Control Measures
Quality control is critical in the production of onsite mixed concrete to ensure that the final product meets the necessary strength and durability standards. Regular testing of materials like aggregates, cement, and water is essential to verify that they maintain consistent quality throughout the mixing process. Sampling should occur at various stages to identify any discrepancies early, allowing for adjustments before the concrete is poured. This step is crucial to avoid potential failures that might occur due to improper material ratios or contamination.
Proper mixing techniques also play a vital role in achieving the desired quality of onsite mixed concrete. It is important to follow specified mixing times to ensure even distribution of materials. Moreover, monitoring the mixing equipment for efficiency and accuracy further enhances the quality of the concrete. Implementing strict protocols for curing and environmental conditions can help maintain the integrity of the concrete, optimizing its longevity and performance in various applications.
Ensuring Consistency and Durability
Onsite mixed concrete in construction projects requires careful attention to detail to maintain quality and ensure durability. The components of concrete must be measured accurately. This involves using precise scales and calibrated mixing equipment. A consistent mix results in better strength and durability of the final product. Regular checks of material properties, like moisture content and aggregate size, contribute to achieving a reliable mix.
Quality control measures play a vital role in the consistency of onsite mixed concrete in various applications. Techniques such as slump tests and compressive strength tests are necessary for evaluating the performance of the concrete. Implementing a systematic approach to mixing, pouring, and curing the concrete helps prevent issues like cracking and shrinkage. Proper training for the crew also ensures that every batch meets the required standards, ultimately leading to longer-lasting structures.
Environmental Impact
Onsite mixed concrete in construction has significant environmental implications. The process typically utilizes local materials, which reduces transportation emissions and energy consumption associated with moving aggregates and cement long distances. Additionally, the ability to produce concrete on-site minimizes waste compared to pre-mixed options. When excess concrete is produced, it can often be reused in other parts of the project, further mitigating waste and the overall environmental impact.
Sustainability is an increasing concern in the production and use of concrete. Onsite mixed concrete in many cases can incorporate recycled materials, such as reclaimed aggregates, which contributes to reducing the demand for virgin resources. Moreover, advancements in technology allow for more efficient mixing processes and the development of eco-friendly additives that enhance the durability of the concrete, making it a more sustainable choice for construction projects. These practices not only improve the life cycle of the structures being built but also contribute to the overall goals of reducing carbon footprints within the industry.
Sustainability Considerations
Onsite mixed concrete in construction offers several sustainability benefits that can contribute to a more eco-friendly building process. By producing concrete at the site, waste can be minimized since the materials are mixed as needed. This reduces the likelihood of over-ordering or leftover materials, which often end up as waste. By carefully controlling the amount of concrete produced, construction teams can significantly lower their environmental footprint.
Furthermore, onsite mixed concrete in projects can utilize local materials, which lessens transportation emissions. This practice not only supports local economies but also decreases the overall carbon impact associated with transporting concrete from distant suppliers. The ability to adjust mix designs in real-time allows for the incorporation of recycled materials, enhancing the sustainability profile of the project while improving resource efficiency.
FAQS
What is site-mixed concrete?
Site-mixed concrete is concrete that is prepared on-site, using the raw materials—cement, aggregates, water, and admixtures—combined in specific proportions to meet project specifications, rather than being pre-mixed in a factory.
What equipment is needed for site-mixed concrete?
Essential equipment for site-mixed concrete includes a concrete mixer, measuring tools for accuracy, shovels for mixing and transporting materials, and a wheelbarrow or similar apparatus for moving the concrete to the desired location.
How can quality control be ensured in site-mixed concrete?
Quality control measures for site-mixed concrete include regular testing of raw materials, monitoring the mixing process for consistency, and conducting slump tests to assess workability and ensuring the final product meets strength requirements.
What are the environmental impacts of site-mixed concrete?
The environmental impacts of site-mixed concrete can include resource consumption, potential pollution from cement production, and waste generation. However, sustainable practices such as using recycled materials and minimizing waste can help mitigate these effects.
Are there sustainability considerations when using site-mixed concrete?
Yes, sustainability considerations include using eco-friendly materials, reducing water usage, optimizing the mix to minimize energy consumption, and implementing waste reduction strategies to lessen the overall environmental footprint of the concrete.