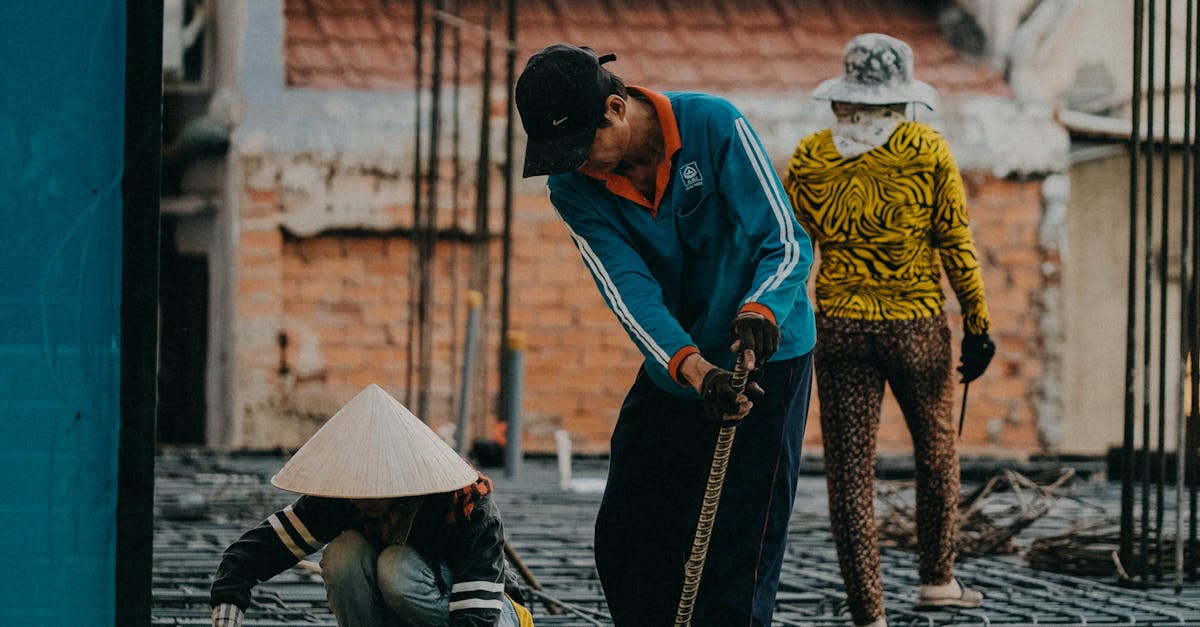
Accessibility Challenges
Mixing concrete on-site presents several accessibility challenges that can hinder the process. Many construction sites are situated in urban areas where space is limited and navigating equipment becomes a logistical nightmare. The need for large mixers and transportation vehicles can be complicated by narrow roads, overhead obstacles, or restricted entry points. These limitations can lead to delays and inefficiencies in the construction schedule.
Onsite mixed concrete in these environments often requires careful planning and coordination to ensure that all materials and equipment can be delivered efficiently. Additionally, sites that are difficult to access may necessitate more manual labor to transport aggregates and mixers, increasing the risk of accidents and time wastage. This enhances the appeal of pre-mixed concrete options, which are delivered ready to use, thereby reducing the complexities associated with on-site mixing.
Location Limitations for On-Site Mixing
Onsite mixed concrete in urban areas often faces logistical challenges due to limited access and space constraints. Construction sites may be nestled between existing structures, making it difficult to maneuver mixing trucks or equipment. The proximity of neighboring buildings can also restrict the placement of bulk materials, which are essential for onsite mixing. These challenges can lead to delays and complications, ultimately affecting project timelines and budgets.
In remote or difficult-to-reach locations, the feasibility of onsite mixing can be even more problematic. Accessibility to water sources and electricity may be limited, which are crucial for the proper mixing process. When transporting materials like cement and aggregates becomes a significant undertaking, relying on pre-mixed concrete from a nearby plant is often a more practical solution. As a result, many construction projects opt for ready-mixed concrete instead of attempting onsite mixing.
Weather Variables
Weather conditions can significantly impact the process of mixing concrete onsite. Extreme temperatures affect the hydration process, which is crucial for the concrete’s strength and durability. In cold weather, the formation of ice crystals can weaken the structure, while in high temperatures, rapid evaporation of moisture can lead to cracking and reduced workability. Both scenarios necessitate careful planning and monitoring to ensure optimal mixing conditions.
Onsite mixed concrete in variable weather can pose challenges for workers as well. Rain can dilute the mix and affect the final product, while wind can hinder the curing process and lead to uneven drying. These factors complicate onsite operations and can lead to delays and increased costs. As a result, using pre-mixed concrete from established suppliers helps mitigate these risks, providing consistency and reliability that onsite mixing may not deliver.
Managing Temperature and Moisture During Mixing
Temperature and moisture management is crucial when dealing with concrete. High temperatures can accelerate the setting process, leading to issues such as cracks and reduced strength. Excess moisture can cause complications like segregation and difficulty in achieving the desired consistency. Onsite mixed concrete in hot or humid conditions requires careful monitoring and possibly the addition of water-reducing agents or retarders to maintain workability.
The fluctuation of environmental conditions adds another layer of challenge. Mixing concrete onsite in colder weather can result in a slower curing process, affecting the overall strength and durability. Specific measures must be employed to manage this, such as using heated mixers or insulating materials. These temperature and moisture control methods can significantly impact the performance of onsite mixed concrete in construction projects, making it essential to understand the implications of the environment on the mixing process.
Equipment Requirements
Onsite mixed concrete in construction requires specialized equipment that can be costly and complex. Mixing trucks, portable mixers, and storage units for raw materials are essential for creating a consistent mix. These tools not only need to be transported to the job site but also maintained and operated correctly to ensure quality control. The logistics of having such equipment readily available could complicate project timelines and resource allocation.
In addition to the equipment, skilled labor is necessary to operate mixers and manage the batching process effectively. Experienced workers understand the precise ratios and mixing times needed to produce strong concrete. Without this expertise, the risk of uneven mixtures increases, leading to potential structural issues. This reliance on professional labor further complicates the feasibility of onsite mixing, pushing many projects towards prefabricated concrete solutions.
The Costs of On-Site Mixing Equipment
The expenses associated with on-site concrete mixing equipment can be significant. Contractors need to invest in mixers, trucks, and other essential tools to ensure proper mixing and delivery. This initial investment often outweighs the benefits, especially when considering maintenance costs and the requirement for skilled operators. The need for frequent repairs and potential breakdowns further adds to operational costs, making this method less appealing for many projects.
Onsite mixed concrete in various construction environments may require additional support, such as power supplies and water sources, which could also contribute to rising expenses. The logistics of transporting and setting up equipment can delay project timelines and lead to increased labor costs. In many cases, purchasing pre-mixed concrete proves to be more economical, allowing contractors to allocate resources more effectively while minimizing operational complexities.
FAQS
Why is it difficult to mix concrete on site?
Mixing concrete on site can present various challenges such as accessibility issues, location limitations, and the need for specialized equipment, which can complicate the process and lead to inefficiencies.
What are the location limitations for on-site concrete mixing?
On-site concrete mixing may be restricted by the available space, proximity to suppliers, and any environmental regulations, making it impractical in certain locations.
How do weather conditions affect on-site concrete mixing?
Weather variables such as temperature and moisture can significantly impact the quality of concrete. Mixing on site exposes the mix to unpredictable weather, which can lead to poor results.
What type of equipment is required for on-site concrete mixing?
On-site mixing requires specific machinery such as concrete mixers, which can be costly to purchase and maintain, adding to the overall project expenses.
Are there cost advantages to mixing concrete off-site?
Yes, mixing concrete off-site can reduce costs related to specialized equipment, labor, and time delays, ultimately leading to a more efficient construction process.