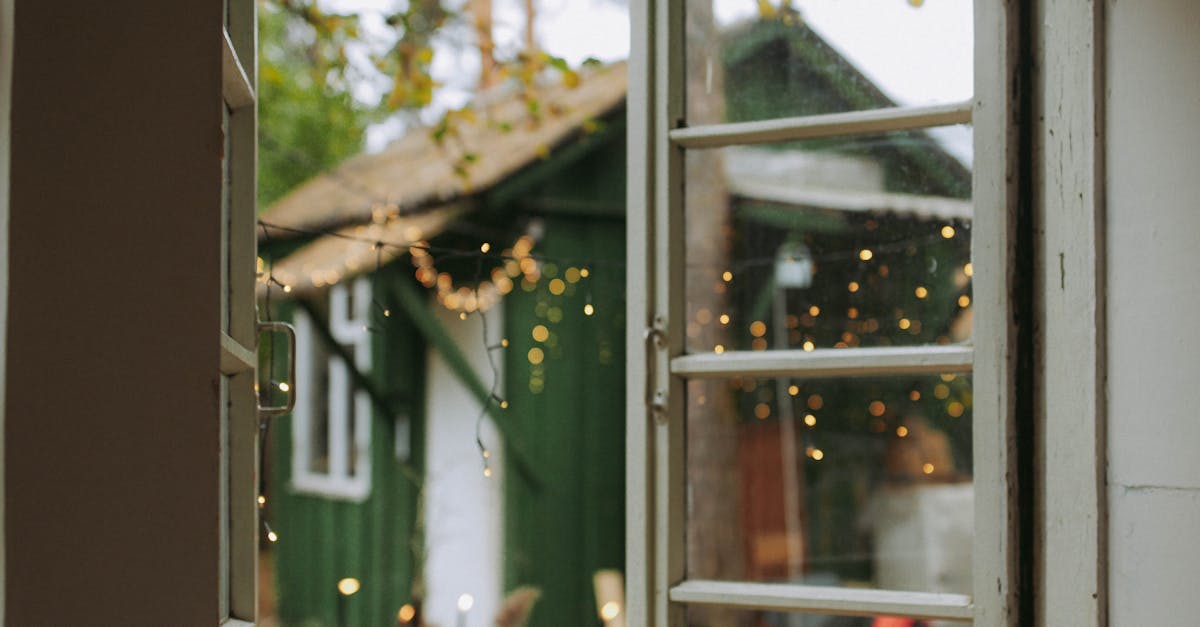
Adding Water to the Mixture
The process of adding water to the mixture is crucial for achieving the desired consistency and workability of onsite mixed screed. Water activates the cement, initiating the hydration process that bonds the aggregates and other materials together. The amount of water must be carefully calibrated to avoid issues such as segregation or drying shrinkage. Too little water may result in a dry mix that is difficult to work with, while too much can weaken the screed, leading to cracks and other structural problems.
When mixing onsite, it is essential to strike the right balance between the various components. Use clean, uncontaminated water that meets industry standards for construction purposes. Gradually adding water while continuously mixing allows for better control over the consistency of the screed. Regular checks during this process ensure that the mixture remains workable, promoting an even application and a smooth finish once installed.
Optimal Water Ratios for Screed
The optimal water ratio for screed is crucial to achieving the right consistency and durability. Typically, the recommended water-to-cement ratio varies between 0.4 to 0.6. This range helps ensure proper hydration of the cement while maintaining the needed workability for placement. Adjusting the water amount within this ratio influences the mixture’s strength and setting time. Onsite mixed screed in residential or commercial settings often requires careful consideration of environmental conditions, such as temperature and humidity, which can affect how water interacts with the dry materials.
Choosing the right water content also impacts the final finish of the screed. Too much water can lead to segregation of the mix, resulting in weak points and reduced overall strength. Conversely, insufficient water can make the mixture too stiff, complicating the application process. Onsite mixed screed in a fast-paced construction environment necessitates accurate measurement and adjustments for the specific project requirements to ensure optimal performance and longevity.
Mixing Techniques for Consistency
Mixing techniques play a critical role in achieving the desired consistency for screed. Whether opting for manual or mechanical methods, the goal remains the same: to create a uniform blend of materials that can be easily spread and shaped during application. Onsite mixed screed in a controlled environment often leads to better results, as it allows for immediate adjustments to the mixture based on real-time observations. A consistent texture will enhance adhesion and final performance, making proper mixing a key focus.
Manual mixing typically involves using a shovel or hoe to combine the materials in a designated area, with labor-intensive effort required to ensure even distribution. On the other hand, mechanical mixing usually employs a concrete mixer or mixing machine, which can provide a more uniform consistency quickly. Onsite mixed screed in larger projects may benefit from these mechanical methods, as they can handle bigger batches and reduce labor time. Regardless of the method chosen, maintaining attention to detail in the mixing process is essential for a successful screed application.
Manual vs. Mechanical Mixing
Manual mixing involves using traditional tools such as shovels and mixing boards to combine the materials. This method allows for greater control over the consistency and can be ideal for smaller batches or confined spaces. Skilled workers can adjust the mixture as they go, ensuring that the right ratios are achieved. Onsite mixed screed in this way often requires more time and physical effort but can lead to a more tailored result that meets specific project needs.
Mechanical mixing, on the other hand, utilizes equipment like paddle mixers or concrete trucks to automate the process. This method is efficient for larger volumes, providing uniformity and reducing labor intensity. The ability to quickly mix large batches can be advantageous on extensive construction sites where time is of the essence. Onsite mixed screed produced with mechanical mixers typically results in consistent quality, though it may lack the nuanced adjustments that come with manual mixing.
Assessing Mix Quality
Assessing the quality of onsite mixed screed is essential to ensure the finished product meets the necessary standards for strength and durability. Key indicators include the mix’s workability, which should allow for easy spreading and leveling. A well-mixed screed will have a uniform color and texture, with no visible dry patches or clumps. Checking for consistency throughout the mixture is crucial, as variation can affect the screed’s performance after curing.
Another important aspect to consider is the screed’s overall fluidity. Onsite mixed screed in a well-balanced hydration state should flow without excessive water pooling or segregation of aggregates. Additionally, performing a slump test can provide insights into the mix’s consistency and water content. Observing the mix for air bubbles and excessive brittleness can also help detect potential issues that might compromise the structural integrity once installed.
Indicators of a Properly Mixed Screed
A properly mixed screed exhibits a smooth and consistent texture, free of lumps or dry patches. This uniformity is crucial for ensuring the screed will cure evenly and provide a strong, stable surface. When assessing onsite mixed screed in this regard, the mixture should flow easily and maintain its shape without collapsing or separating, indicating the correct balance of materials has been achieved.
Another important indicator is the moisture content of the screed. If the mixture appears too wet, it may lead to issues such as shrinkage or weakness after curing. Conversely, a mixture that is too dry can result in poor adhesion and increased susceptibility to cracking. Onsite mixed screed in optimal conditions will exhibit a workable consistency that holds its shape while still retaining sufficient moisture for effective bonding.
FAQS
What materials are needed to mix screed on site?
To mix screed on site, you will need cement, sand, water, and any additives if required. Make sure to have the appropriate mixing tools, such as a shovel or a concrete mixer, depending on the volume you need to prepare.
How do I determine the optimal water ratio for my screed?
The optimal water ratio generally depends on the specific mix design and the type of screed being used. A common guideline is to use about 0.4 to 0.5 liters of water per kilogram of cement. However, it’s essential to refer to the manufacturer’s specifications or industry standards for precise ratios.
What is the difference between manual and mechanical mixing of screed?
Manual mixing involves using tools like shovels or hand mixers to combine materials, which is suitable for small batches. Mechanical mixing uses a concrete mixer or other machinery, providing a more consistent mix and saving time, especially for larger quantities.
How can I tell if my screed mix is of good quality?
Indicators of a properly mixed screed include a uniform color and texture, a workable consistency (not too dry or too wet), and the absence of lumps or unmixed materials. You should also perform a flow test to ensure it spreads evenly.
What should I do if my screed mix is too wet or too dry?
If the mix is too wet, you can add more dry ingredients, like sand or cement, to achieve the right consistency. If it’s too dry, slowly add small amounts of water while mixing until you reach the desired texture. Remember to mix thoroughly after any adjustments.